Pour compléter le test live sur le forum, voici une revue détaillée qui vous permettra de découvrir l’imprimante Original Prusa XL en version cinq têtes. Sortie après une très longue attente de plusieurs années, retardée en partie par la période de pandémie, cette machine de l’entreprise Prusa Research fait déjà l’objet d’évolutions. C’est de cette “nouvelle version” dont notre test parle aujourd’hui.
Fiche technique de l’Original Prusa XL 5T
Voici un résumé synthétique des spécifications de la machine. Nous détaillerons les éléments clés un peu plus loin dans ce test de la Prusa XL.
Technologie | FDM avec cinématique CoreXY à changement d’outils |
Volume maximal d’impression | 360 x 360 x 360 mm |
Hauteur de couche | De 50 à 300 microns (buse 0.4 mm) |
Type d’extrudeur | Changeur d’outils à 5 têtes Direct Drive “Nextruder” avec une démultiplication de 1:10, compatible E3D V6 |
Température maximale de la buse | 290°C |
Température maximale du plateau | 120°C, chauffe uniquement la zone de l’objet à imprimer |
Vitesse maximale d’impression | Non communiquée |
Nivellement du plateau | Capteur de force, uniquement sur la zone de l’objet à imprimer |
Filaments compatibles | PLA, PETG, Flex, PVA, PC, PP, CPE, PVB |
Filaments compatibles avec enclosure | ABS, ASA, HIPS, PA |
Connectivité | Clé USB, Ethernet et WiFi |
Dimensions | 70 x 90 x 72 cm |
Poids | 33.7 kg |
Consommation électrique | Paramètres PLA : 80W / Paramètres ABS : 120W |
Concurrence | N/A |
Cette Original Prusa XL possède le plus gros volume d’impression de la marque, quatre fois supérieur à la MK4S et huit fois supérieur à la MINI+. On retrouve la plateforme xBuddy 32-bit commune aux Original Prusa MK4/S, MK3.9/S, MK3.5/S, MINI/+ et bien entendu la XL.
Toutes les fonctions devenues pratiquement standards de nos jours sont de la partie : la connectivité réseau local et cloud, la détection de crash, la reprise après coupure de courant, la détection de fin de filament.
L'imprimante Originale Prusa XL 5T sur le comparateurDéballage (unboxing)
Il est bon d’éclaircir toutes les variantes possibles lors de la commande de l’Original Prusa XL. On peut composer une combinaison de trois éléments :
- Le nombre de têtes : 1, 2 ou 5
- Assemblée ou semi-assemblée
- Avec le kit caisson ou non
Le présent test concerne une Original Prusa XL en variante 5 têtes, semi-assemblée, sans kit caisson. Elle est livrée en deux cartons. On peut s’en sortir tout seul pour la manutention mais il vaut mieux être deux personnes pour déplacer le gros colis (35kg !) et même pour le vider de son contenu.
Le carton le plus volumineux contient toute la machine avec deux têtes, les trois têtes restantes sont dans le second carton plus petit.
Montage de la XL et de ses 5 extrudeurs
Précisions
Pas de photoreportage détaillé des étapes de montage ici, juste les grandes lignes. Cette machine est sortie il y a assez longtemps et cette partie est déjà très bien couverte. En plus du manuel en ligne en version anglaise riche de commentaires utiles (voir ici pour le français), on trouve facilement des vidéos complètes du montage et même en temps réel.
Il faut cependant préciser un point important. La version assemblée n’est en réalité pas totalement assemblée. Il y a tout de même quelques étapes de montage à effectuer pour finaliser l’assemblage de la machine, multipliées par le nombre de têtes. Ce n’est pas juste un déballage et une mise en route comme avec des produits concurrents affichés comme “assemblés”.
Dans la même veine, le modèle « semi-assemblé » ne signifie pas non plus qu’il n’y a qu’à visser trois morceaux ensemble et commencer à imprimer vingt minutes après, loin de là ! Le montage s’est effectué en deux après-midi, du déballage à la première impression en passant par les calibrations. C’est donc faisable en une journée sans se presser. Vu la quantité de travail, cette version semi-assemblée pourrait tout à fait être qualifiée de « kit ».
Préparation
Prévoyez un espace de travail bien dégagé mais contrairement à ce que l’on pourrait croire pour une machine de cette dimension, il n’est pas nécessaire d’avoir un plan de travail de cinq mètres. Une table six places fera très bien l’affaire en prévoyant autant d’espace au sol pour les cartons.
Pour travailler confortablement, il faut pouvoir poser le châssis complet de la machine sur la table, ainsi que toute la visserie bien étalée et triée à côté. Prévoyez un petit récipient pour les pièces en spare, cela vous débarrassera rapidement des petits sachets et vous y verrez plus clair. Si vous avez un plateau de tri, c’est encore mieux car pas mal de sachets de visserie ne sont pas zippables.
Montage
Le montage commence par la base du châssis sur laquelle il faut fixer les profilés en alu. On sent bien qu’on est dans un autre monde mécaniquement par rapport aux modèles tels que la MK4S. Les pièces mécaniques sont de haute qualité, avec plein d’éléments usinés, rectifiés, anodisés. La précision est juste incroyable, les assemblages sont fermes et étudiés pour être le plus rigide possible. Il n’y a d’ailleurs pas de jeu du tout, simplement parce que les profilés qui s’emboîtent doivent rentrer en force. C’est-à-dire qu’il y a une sorte de tenon qui doit mordre dans le métal au fur et à mesure que l’on serre les vis, aidé par l’outil de mesure du couple de serrage.
On vient ensuite monter l’écran xLCD. Il s’agit du même type d’écran que toute la famille partageant la même plateforme 32-bit, par exemple la MK4S. Il faut faire passer un fil de terre ainsi que la nappe de l’écran par l’intérieur de la rainure des profilés, sur tout le pourtour du châssis depuis l’avant bas jusqu’à l’arrière haut. Cela fait une bonne longueur de câbles et ce n’est qu’une fois arrivé à la carte mère que je me rends compte que j’ai pris un peu trop de mou au début et que le fil de terre est trop court… Allez hop, on démonte et on recommence… Heureusement, ça va beaucoup plus vite lorsqu’on l’a fait une fois.
Au passage, la fonctionnalité tactile est activé, ce qui n’était pas le cas à la sortie de la MK4.
Vient maintenant la pose du fameux assemblage CoreXY, des rails Z, puis le panneau arrière avec l’électronique et les trois alimentations (pour la version 5T), avant de fixer le plateau chauffant ou plutôt le multi-plateau. Jusque-là tout va bien, on suit tranquillement et méthodiquement les étapes du guide.
Pro-tip : il est très pratique de bloquer les patins des rails Z à mi-hauteur en réutilisant les petits clips verts le temps du montage, pour éviter d’avoir les pattes de fixation du plateau dans le chemin de la clé lors du serrage des vis, ça libère une main.
On peut enfin monter les Nextruder en commençant par fixer leurs docks d’amarrage. C’est une étape qu’il faut aussi effectuer sur la version « assemblée ». Au moment du montage, il y avait 47 commentaires de plainte pour cette étape, au moins on sait tout de suite que ça ne va pas être évident. Et en effet, cette étape a été la plus compliquée à réaliser.
On est censé serrer les docks de la même manière que pour les profilés du châssis, c’est-à-dire qu’un tenon (entouré ci-dessous) doit mordre le métal du profilé alu. Le manuel précise qu’il faut serrer très fort et que ça ne doit pas bouger d’un poil, il y a même une vidéo qui montre comment ça doit être rigide.
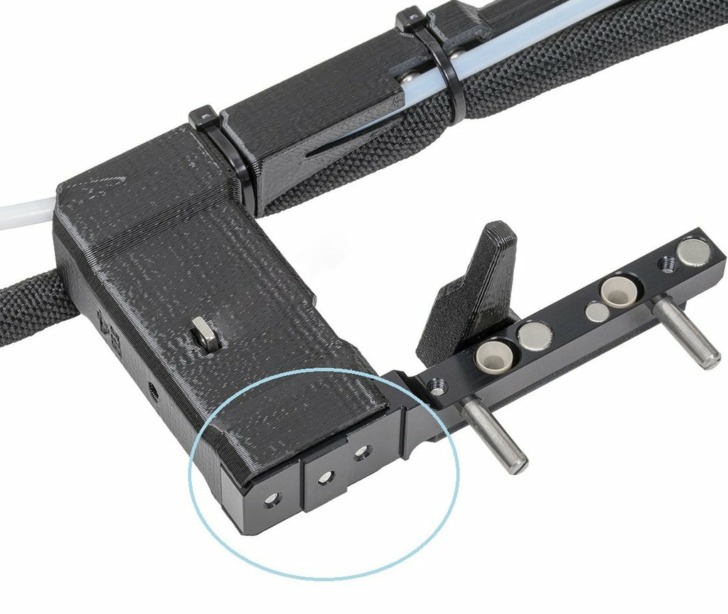
Pour la structure du châssis, c’étaient des vis M4 avec une clé six pans que l’on tenait du côté long et on était assisté par un outil de mesure du couple. Là où c’est compliqué ici, c’est qu’il s’agit d’une petite vis M3 par dock, avec une empreinte six pans standard et non Torx, et qu’on est censé la serrer en utilisant la boule, donc en tenant la clé par le côté court. Le tout en passant à travers la grille en nid d’abeille à l’arrière…
Pour procéder au montage, j’ai utilisé une clé longue avec un manche (comme un tournevis) afin de bien sentir l’effort appliqué. J’ai passé un bon quart d’heure sur le premier dock, en serrant plus que de raison à mon goût, sans obtenir la rigidité souhaitée. Ce n’est qu’au deuxième que j’ai trouvé une technique. A partir de là, il faut moins d’une minute par dock pour terminer le montage. J’ai remonté le premier dock suivant la même technique et j’ai obtenu la même rigidité que les autres. Cette étape mériterait vraiment d’être améliorée.
Une fois ce passage difficile franchi, on déroule le reste du manuel d’assemblage, sans plus d’accroc. Montage des accessoires, supports de bobine, antenne wifi etc… Ce sont là encore des étapes à effectuer sur la version assemblée. Au passage on aura remarqué quelques détails intrigants, notamment un sixième connecteur “Dwarf” qui est le connecteur de tête d’impression…
On n’oubliera pas d’effectuer une étape de graissage qui est discrètement indiquée dans le manuel.
Pour résumer le montage, j’ai trouvé que les éléments pré-assemblés étaient dans l’ensemble du niveau de qualité et de simplicité attendu pour une Prusa. Je l’ai trouvé dans l’esprit maker malgré tout, plus que le montage de la MK4 qui comportait plusieurs passages sensibles qui sont tous pré-assemblés sur la XL. Petit bémol cependant sur la fixation des docks où on est un cran en dessous, avec risque de casse si l’on s’y prend mal, ou du moins c’est l’impression que cela donne.
Côté pratique, les deux grosses poignées intégrées sont bien placées pour déplacer la machine depuis le sol. Mais si on veut la déplacer sur une table, c’est plus compliqué car les poignées sont trop hautes.
En la prenant par l’arrière, le poids est très bien équilibré, proche du corps, ce qui permet de la manipuler tout de même assez aisément malgré son encombrement et son poids. Pour l’anecdote, la Prusa XL5T, bien que d’apparence massive (voir le Benchy sur la photo ci-dessous pour l’échelle), occupe moins de surface sur un bureau que sa cousine la MK4S/MMU3 + buffer + supports de bobines.
Mise en route de la Prusa XL
Vient enfin le moment tant attendu, la première mise sous tension. Autant vous le dire tout de suite, il faudra avoir le bras long : le bouton marche/arrêt se situe à l’arrière de la machine. Avec les bobines chargées sur les portes bobines de droite, ce bouton est très difficile d’accès. Cela devient un problème récurrent chez Prusa.
Mon modèle était pré-chargé avec la version 6.0.0 du firmware mais la version 6.0.4 qui était la dernière en date au moment du montage était déjà présente sur la clé USB. Il suffit d’allumer la machine avec la clé USB connectée et de confirmer l’exécution de la mise à jour.
Même si l’on peut encore s’aider du manuel de montage, l’assistant de calibration vous prend par la main et détaille chaque étape sur l’écran avec des illustrations. Prusa a effectué un remarquable travail de simplification, l’utilisateur n’a qu’à effectuer les actions demandées, l’une après l’autre. Dévisser ici, resserrer là, attention à retirer les doigts avant la prochaine étape car la machine se mettra en mouvement, toucher la buse sans crainte elle est froide, etc…
A noter que par défaut, le côté gauche de la machine accueille trois bobines et deux sur le côté droit. L’assistant de mise en route propose de déplacer la troisième bobine à droite mais si vous le faites, le bouton marche/arrêt sera tout à fait impossible d’accès depuis l’avant de l’imprimante lorsque les bobines seront chargées. Imaginez cette photo avec trois bobines chargées.
La calibration des offsets sur les cinq têtes prend environ quatorze minutes mais est entièrement autonome. Elle utilise une pige de calibration, que l’on visse au centre du plateau et qui sert de référence. Une fois la calibration terminée, on peut ranger la pige sur un des capteurs de filaments afin de toujours l’avoir à portée de main, sans l’égarer.
La Prusa XL est désormais prête au service. Il est temps de mettre la tôle flexible satinée et d’envoyer les premières impressions, sans plus tarder.
Impressions de test (PLA)
Première impression, première leçon
Première déconvenue… La Prusa XL était connue pour ce genre de problèmes, qui devaient être corrigés grâce entre autres à PrusaSlicer 2.7.0-beta1 et au passage à des buses en 0.4 mm. Il faut croire que ce n’est pas suffisant ici. En palliatif rapide, voici la même impression test en utilisant une température de 200°C.
C’est nettement mieux mais le problème de fond n’est pas résolu. Il apparaitra régulièrement durant les tests suivants. Ce n’est qu’après pas mal d’essais et de recherches (détaillés sur le forum) que l’on apprendra la première leçon : pour les impressions multi-couleur sur la Prusa XL, il est impératif de sécher les filaments.
Impression test aux limites d’axes
On ne peut évidemment pas passer à côté, il faut tester les dimensions limites au moins une fois. Ici en X et Y sur 360 mm.
Ca imprime vraiment au bord et la première couche est parfaite. La grande feuille a été imprimée sans nettoyage préalable du plateau, on y voit les traces de doigts et d’anciennes impressions.
Et ici en Z, toujours sur 360 mm. Nous reverrons la boule plus loin.
Impression grande échelle
On envoie une impression de 36 cm de haut et cinq couleurs. Basé sur le profil 0.15 mm SPEED avec quelques ajustements, cette impression de 415 grammes a duré 16h30.
A côté du sapin se trouve sa tour de remise en pression de seulement trois grammes, qui était au fond durant l’impression. Elle est minuscule car la fonction “No sparse layers” a été utilisée. Elle permet de réduire la tour aux couches où il y a des changements de couleur uniquement, parfaitement adapté à ce type d’objet. Cela impose d’avoir de la place pour que la tête d’impression puisse redescendre sur la tour et changer d’outil sans collision avec la pièce. Ici, le plateau de la XL est de taille confortable pour permettre l’utilisation de ce type de fonction, même sur une grosse pièce.
Le passage critique de cette impression est le beau surplomb juste après le tronc, que la ventilation de la XL a réussi à gérer comme elle l’a pu. C’est granuleux, mais il n’y a rien qui pendouille.
Hormis pour le surplomb, on notera l’excellente qualité d’extrusion.
Ainsi que la première couche parfaite, vraiment parfaite sur toute la surface de la base de 20 centimètres de diamètre.
Logiciels
PrusaSlicer
PrusaSlicer que vous pouvez télécharger ici est un slicer open source qui a une bonne popularité; tellement qu’il sert de base aux concurrents. Gratuit et activement développé par Prusa Research, il est originellement basé sur Slic3r d’Alessandro Ranellucci et la communauté RepRap. PrusaSlicer n’est pas verrouillé aux machines de la marque et comporte des profils pour de nombreuses imprimantes (Anycubic, Creality, Flsun, Ultimaker…).
L’arrivée de la Prusa XL dans le catalogue du constructeur a fait apparaitre de nombreuses évolutions dans les dernières versions de PrusaSlicer, ceci pour tenir compte des particularités des imprimantes multi-couleurs et surtout multi-têtes. La tour de purge a notamment été complètement revisitée. Il possède également une fonction de peinture rendant assez aisée la transformation d’un modèle monochrome en un modèle coloré.
Pour imprimer un fichier G-Code généré par PrusaSlicer, vous avez l’embarras du choix : via la clé USB, via le port USB par OctoPrint par exemple, via PrusaLink ou encore via PrusaConnect. Pour ces deux dernières méthodes, si une série d’impressions est planifiée, il est possible de toutes les télécharger d’avance en file d’attente. Une fois devant l’imprimante, il suffit de la marquer comme “prête” sur l’écran quand les bons filaments sont chargés et le plateau nettoyé pour passer au job suivant.
PrusaLink
PrusaSlicer peut se connecter à une “imprimante physique” en réseau via l’interface PrusaLink. Il s’agit ici uniquement d’une solution réseau local qui peut fonctionner en vase clos et qui n’a aucunement besoin de cloud ou d’internet pour fonctionner. C’est intéressant pour un réseau d’entreprise, par exemple.
PrusaLink donne la possibilité, depuis PrusaSlicer, de faire un vrai “Click to Print”. La clé USB reste nécessaire et doit rester connectée sur la machine mais n’a plus à être manipulée.
Une interface web est directement disponible sur l’imprimante afin de pouvoir visualiser son état (uniquement les paramètres essentiels), visualiser le contenu de la clé USB et télécharger des gcode dans les deux sens. Bien entendu, il est possible de démarrer et d’arrêter une impression depuis cette interface. Pas de fonctions avancées cependant, c’est le minimum fonctionnel : pas de caméra, pas de préchauffage, pas de mouvement possible.
PrusaConnect
PrusaConnect, est directement intégré dans un onglet de PrusaSlicer. Dès que vous connectez votre compte Prusa, l’onglet apparait dans le logiciel trancheur.
C’est la version cloud qui propose une interface web bien plus riche. On peut contrôler la machine, récupérer toutes les données télémétriques sous forme de graphiques en temps réel, stocker gratuitement jusqu’à 1 Go de fichiers G-Codes. On peut aussi retrouver la “caméra” si on en a intégré une, il y a plusieurs moyens pour le faire. Comme pour la Prusa MK4, l’imprimante ne gérant pas de caméra en natif, cette possibilité ne sera pas testé dans ce test de la Prusa XL.
J’ai testé PrusaConnect avec un parc de trois modèles différents de Prusa. L’intérêt est du coup assez limité puisque les G-Codes sont spécifiques pour chaque modèles de machine, c’est plus intéressant pour une ferme d’imprimantes identiques. Je trouve assez dommage qu’un 3MF du projet PrusaSlicer ne soit pas stocké sur le cloud avec le G-Code, qui permettrait de le retrancher facilement pour un autre modèle de machine.
Les fichiers transmis au cloud doivent être téléchargés vers la clé USB de l’imprimante. Le transfert pouvant prendre un peu de temps, l’imprimante démarre l’impression avant même d’avoir reçu l’intégralité du G-Code.
PrusaConnect est bien entendu accessible partout, il existe même une application Android vous permettant de garder un œil sur votre parc de machines et de recevoir des notifications. C’est assez sympa que PrusaSlicer propose aussi d’utiliser PrusaConnect comme interface d’imprimante physique, comme pour PrusaLink. Il est ainsi possible par ce biais d’utiliser le même type de “Click to Print” depuis n’importe où, sans avoir besoin d’être connecté au réseau local.
D’autres impressions de test avec la Prusa XL 5T
PLA
Un benchy Voronoï.
Un vase utilisant une technique de tramage.
Une astuce intéressante consiste à utiliser un filament différent pour le remplissage. L’intérêt est d’économiser le filament visible et d’utiliser un filament plus économique pour la partie non visible. Bien entendu, il faudra adapter cette technique à votre besoin, en fonction des pertes dans la tour et en temps d’impression. Cette démo très optimisée montre aussi combien il est possible de réduire les déchets dans la tour, sans la désactiver.
Une impression pour le fun, le logo du site dans une position parfaitement optimale.
Et enfin, une dernière petite impression toute en PLA : un Benchbin.
C’est une impression multi-couleurs qui permet de tester pas mal de choses :
- Adhérence au plateau
- Qualité de la première couche
- Qualité de l’extrusion
- Ponts sans support
- Tolérance sur les pivots imprimés “in place”
- Temps d’impression
Elle a duré environ 11h30 et nécessité quelque chose comme 1150 changements d’outils. Un total de 190 grammes dans la pièce et 50 grammes dans la tour pour ~12 cm de hauteur. Le profil utilisé est le 0.20 mm SPEED, celui qui privilégie la vitesse à la qualité, notamment sur les périmètres extérieurs.
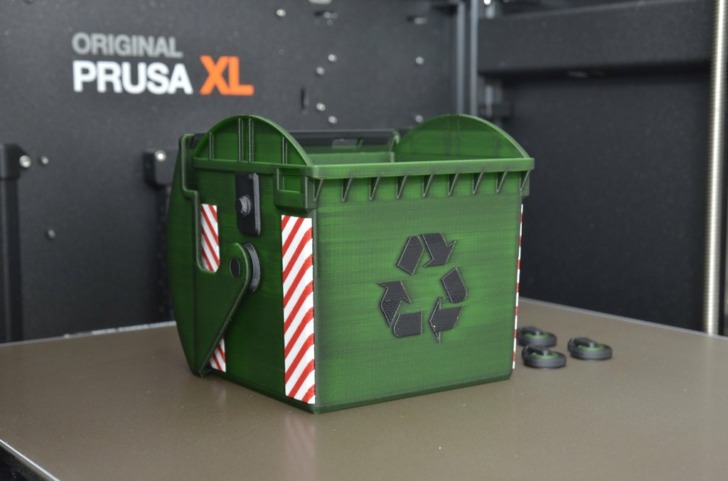
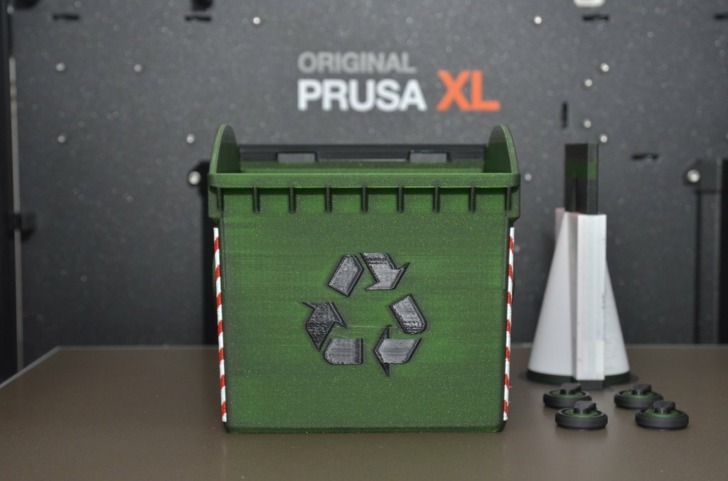
Pour ce qui est de la première couche, de l’adhérence au plateau et des tolérances, on est bon. Pour la qualité d’extrusion en revanche, il y a des manques dans les bandes rouges et dans le logo recyclage. Peut-être imputables au profil SPEED utilisé.
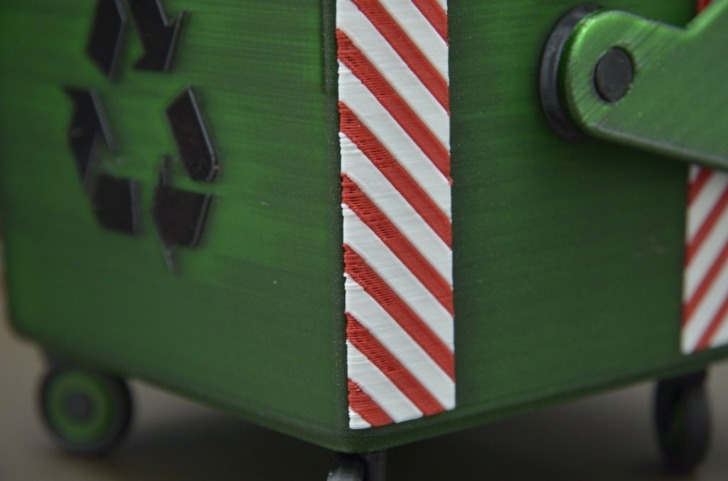
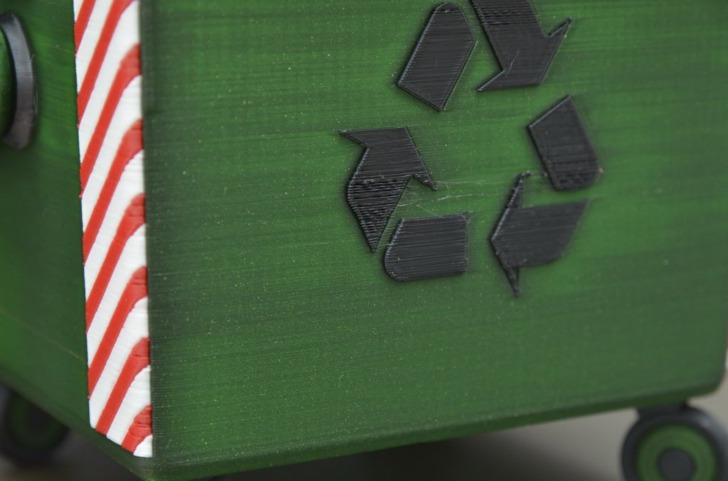
PLA / PETG
Le point fort de cette machine est la possibilité de mélanger les types de filament sans contamination croisée. Le couple le plus populaire est l’utilisation du PLA comme support pour le PETG (et vice-versa).
Nous avons ici imprimé une boule en PETG supportée par du PLA, en utilisant un profil « supports solubles ». Ce profil permet d’imprimer directement sur le support sans ménager d’espace et ainsi d’obtenir un état de surface très propre sous les supports.
Ces deux matières n’adhérant pas entre elles, cela permet au support de se détacher facilement sans laisser de trace.
Même chose pour ce petit bouchon dôme incluant un pas de vis.
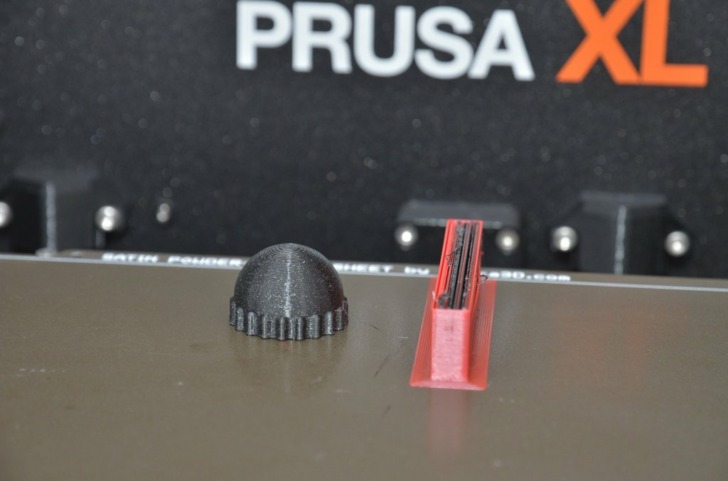

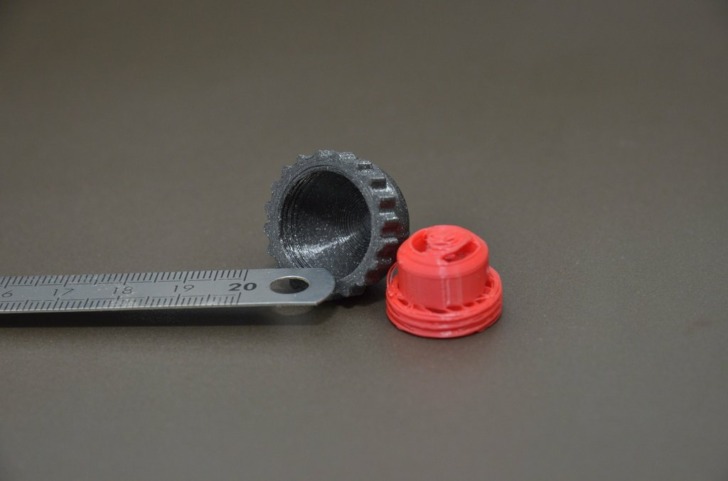
Une autre impression ayant bénéficié de ce principe, mais cette fois-ci les supports sont en PETG pour des pièces bicolores en PLA.
Les supports se détachent très facilement et la qualité des surfaces supportées est tout bonnement parfaite. La partie orange a été peinte dans PrusaSlicer, d’un clic de remplissage intelligent. Le résultat obtenu est meilleur et bien plus simple que si la pièce avait été conçue en deux STL séparés.
Des Yoshi en PLA avec support PETG
Production d’une petite série en PLA/PETG.
L’impression aura duré environ 26 heures pour un demi-kilo de PLA et seulement 23 grammes de supports en PETG. La tour de remise en pression ne fait que 3 grammes. On notera l’excellente qualité de surface sous les supports.
L’Original Prusa XL a fait du très bon boulot ici, imprimer de la série sur un plateau bien rempli ne lui pose aucun problème.
J’en profite pour indiquer qu’il existe une fonctionnalité intéressante lorsque l’on imprime des grosses séries. Si vous lancez une série et qu’une pièce en particulier pose problème, il n’est pas nécessaire d’arrêter toute l’impression, il est possible d’annuler l’objet concerné et l’imprimante sautera simplement le G-Code associé.
PETG
Une autre petite série ici : 80 bouchons de vis en PETG.
TPU 95A / PLA
Le TPU est une matière qui colle très fortement au plateau, quel que soit son type. Bien qu’il soit possible de l’imprimer directement sur le plateau, nous allons mettre à profit le multi-tête et utiliser une première couche en PLA qui servira d’interface de séparation. Tant que nous y sommes, nous utilisons aussi le PLA comme support.
L’utilisation de supports en PLA permet d’avoir des surplombs très propres, impossibles à obtenir en impression mono-matière. Les supports PLA se détachent très facilement du TPU.
ASA
L’impression en ASA peut être délicate pour plusieurs raisons. L’adhérence peut être trop forte sur certains types de plateaux, notamment le PEI lisse. Malgré cela, c’est une matière sujette au warping.
Afin de tenter de pallier ce problème d’adhérence trop forte, nous allons reprendre le principe utilisé pour le TPU et nous servir d’une première couche dans une autre matière qui servira d’interface de séparation. Première tentative avec un raft en PLA.
Le PLA se détache très facilement de l’ASA mais nous remarquons ici qu’il n’est pas adapté car il s’est déformé sous la tension générée par l’ASA. Deuxième tentative en utilisant du PETG et une seule couche plutôt que tout un raft.
On remarque que l’ASA tire toujours dans les angles mais le PETG tient bon. A noter que l’on peut imprimer directement de l’ASA sur le plateau satiné, sans colle.
D’autres pièces en ASA.
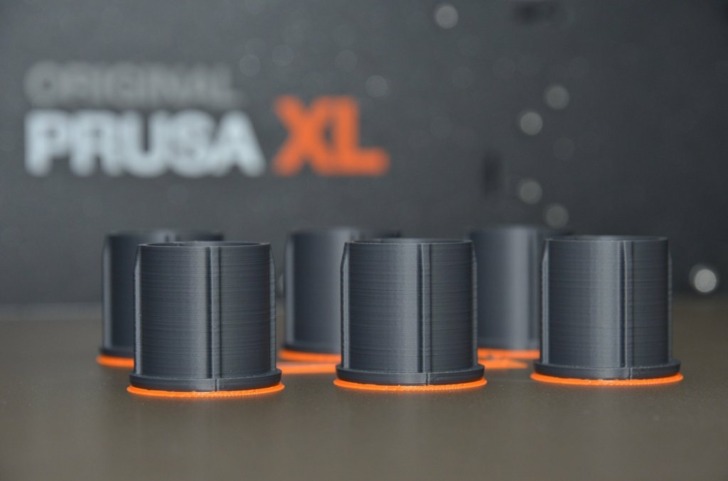
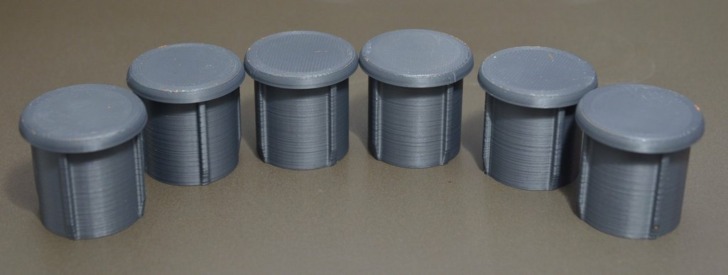
Ces pièces sont relativement petites. Une autre tentative avec une pièce plus grosse, d’environ 13 cm de côté, a été avortée à cause d’un warping important. La machine était pourtant dans un bureau fermé, à l’abri des courants d’air. Pour faire des pièces plus importantes, il faudra impérativement mettre l’imprimante sous caisson, par exemple avec le “Original Prusa XL Enclosure“. C’est d’ailleurs précisé dans les spécifications, plutôt dommage pour ce type de machine.
Autres
Nous avons ensuite une petite pièce technique imprimée en PC Blend, avec son joint torique en TPU, utilisant des supports en PLA pour les deux. Pas de problème sans caisson, la pièce étant petite.
Comparaison MK4 & MMU3 vs XL5T
Sur toutes les comparaisons ci-dessous, on a sur la gauche la Prusa MK4 avec son MMU3 et sur la droite la Prusa XL 5T (5 têtes). Ces photos sont faites pour mettre en évidence cette différence et il faut déjà regarder de très près à l’œil nu.
Pour le Yoshi ci-dessous, la MK4 & MMU3 montre un léger mélange des couleurs, le blanc et le rouge sont un peu plus sombres mais la XL5T montre une très légère peau de saumon.
Plusieurs impressions comparatives en simple extrusion, en 0.20 mm et 0.15 mm, ne montrent pas de différence significative entre les deux machines. Selon le détail observé, parfois l’une sera devant, parfois ce sera l’autre.






Mon appréciation personnelle tend vers la MK4 que je trouve plus homogène mais encore une fois, les photos sont prises de manière à rendre visibles les petits défauts. Je passe de longues minutes à la loupe x4 pour voir les différences… Cela démontre bien que la Prusa XL5T jouit d’une qualité d’impression exceptionnelle, très proche de celle que l’on connait avec la Prusa MK4.
J’ai remarqué également que les impressions de la XL5T sont globalement plus brillantes que celles de la MK4, à température égale. Je pense qu’il y a deux raisons à cela :
- La XL5T est équipée de chaussettes en silicone que n’a pas la MK4 (mais la MK4S oui)
- Le flux de refroidissement est dirigé sur la sonde de température pour la XL5T et sur la buse pour la MK4. On en reparle dans le chapitre ci-dessous.
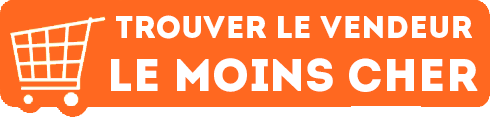
Revue technique
Mise en garde
Il est toujours bon de rappeler qu’une imprimante 3D est une machine comportant des pièces en mouvement et des zones pouvant chauffer à plusieurs centaines de degrés. Il y a donc un risque possible de blessure. C’est d’autant plus important d’être vigilant sur cette grande machine ouverte, complexe, qui effectue des mouvements amples et rapides en manipulant des têtes d’impressions brûlantes.
Si la plupart du temps, un maker sait où ne pas mettre les doigts, je me suis fait surprendre une fois avec cette Prusa XL lors de la purge en bordure de plateau avec un filament particulièrement baveux. Ma main trainait sous le plateau et a reçu une goutte de plastique fondu qui m’a value une petite brûlure. Maintenant, je le sais et je fais attention mais c’est la preuve qu’il faut toujours prendre garde, à plus forte raison sur cette imprimante qui n’est pas fermée d’origine.
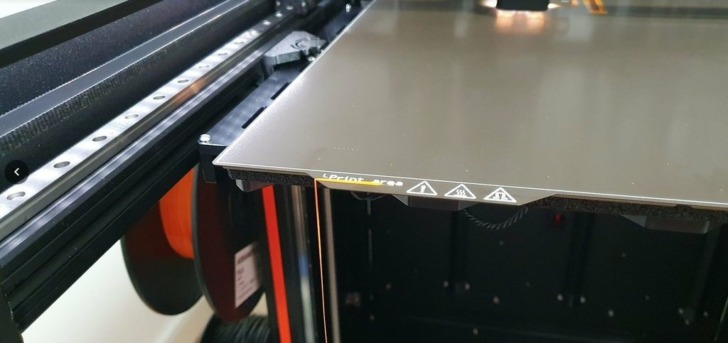
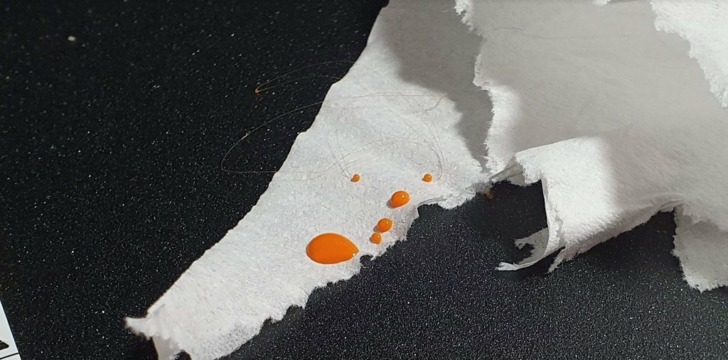
Cinématique CoreXY
La cinématique CoreXY repose toujours sur un système de coordonnées latitudinales et longitudinales, à l’instar des cartésiennes. Le déplacement des axes X et Y est toujours assuré par deux moteurs mais la différence d’une CoreXY est que les mouvements X et Y dépendent l’un de l’autre. Faire tourner un seul moteur entraine un mouvement diagonal de la tête.
Les moteurs sont fixes, simplifiant le câblage. Les axes X et Y sont beaucoup plus légers, ce qui permet virtuellement des impressions plus rapides sans les artefacts dus au poids du plateau comme sur une bed slinger (plateau mobile en Y). La conception permet également un gros gain de place sur l’axe Y car le plateau ne bouge qu’en Z.
Les courroies utilisées dans les imprimantes CoreXY sont beaucoup plus longues, ce qui rend tous les problèmes de courroie plus importants qu’avec les imprimantes cartésiennes. Leur chemin compliqué rend également ces problèmes plus difficiles à réparer. Le cadre doit être très stable et parfaitement perpendiculaire, sinon la précision dimensionnelle sera inférieure.
Toolchanger
Un toolchanger est par définition un mécanisme permettant de changer d’outils, ici des têtes d’impression. Pour ce faire, la Prusa XL utilise un chariot mobile très léger équipé d’un mécanisme de préhension passif très astucieux. Ce système ne nécessite aucun actionneur pour verrouiller et déverrouiller les outils ou les placer au parking.
Le parking, justement, est composé de docks auxquels les têtes d’impression sont accrochées. On voit ici le parking où la tête numéro trois est manquante car chargée sur le chariot mobile.
Les buses sont obturées par une languette anti-oozing dont la hauteur est réglable, ce qui nous amène à une particularité des systèmes qui utilisent plusieurs têtes d’impression : les têtes inutilisées doivent baisser leur température pour ne pas dégrader le filament. Cet aspect est géré par PrusaSlicer qui possède un paramètre réglable de température de veille.
Une température de veille même réglée aussi basse que 70°C par exemple, sur une période prolongée, aura un effet similaire à un séchage. Par conséquent, l’humidité qui s’est échappée du filament à l’intérieur de la hotend se retrouve prisonnière et finira par faire baver le filament lors de la sortie de parking. C’est l’une des raisons pour lesquelles il faut utiliser des filaments parfaitement secs pour l’impression multi-têtes.
Têtes d’impression (Nextruder)
Les têtes d’impression de type “Nextruder” (que l’on ne présente plus) sont un condensé de technologie. Un moteur pancake surmonté d’une réduction planétaire de 1:10 assure l’entrainement du filament grâce à une large roue dentée qui grippe fortement le filament en appui contre deux roulements à gorge.
Filament qui passe par un second capteur à effet Hall (analogique) en plus de celui positionné sur les côtés à l’entrée des tubes PTFE. La température du heatsink est régulée grâce à son ventilateur asservi par une sonde de température logée dans le radiateur. Le ventilateur de la hotend se voit attribué une écope pour aspirer l’air à l’opposé du plateau chauffant, ce qui est une très bonne idée.
Le radiateur est la pièce centrale du Nextruder. Il s’agit d’un grand dissipateur thermique en aluminium, qui intègre dans son cœur une jauge de contrainte (un capteur de force). Sa précision et sa sensibilité sont telles que l’imprimante est en mesure de déterminer si la buse n’est pas totalement propre pour effectuer correctement le palpage du plateau. C’est assez impressionnant à voir.
D’autres capteurs permettent de connaître la position exacte de la tête, si elle est sur le dock ou si elle est sur le chariot mobile, voire même s’il y a un problème. Un retour lumineux en façade indique l’état de la tête.
Sur la Prusa XL5T, les têtes d’impression sont facilement déconnectables. Il s’agit de débrancher le connecteur unique, retirer le tube PTFE de son pneufit et de desserrer les deux vis de maintien du guide câbles en plastique. Vous pouvez ainsi très simplement effectuer la maintenance d’une tête sur une table.
Les buses du Nextruder sont longues et tout-en-un. Le tube faisant office de heatbreak est une partie intégrante de la buse, il n’y a pas de fuite possible ni de serrage à chaud à effectuer. Ce tube traverse tout le radiateur jusqu’au plus près de la roue dentée d’entrainement du filament.
Le refroidissement de la pièce s’appuie sur un ventilateur radial très fin de type 5010.
Le flux d’air est étonnamment orienté puisqu’il traverse toute la longueur du corps de chauffe avant d’atteindre la buse. L’air est donc chauffé avant d’atteindre la pièce et le gradient de température fait que la buse a toujours une température légèrement supérieure à celle que voit la sonde, ce qui peut expliquer que les pièces soient plus brillantes que sur une MK4 à température égale. Notez la présence de deux puissantes LEDs blanches qui éclairent la buse.
Pour comparaison avec la MK4 et la MK4S, le flux d’air passe d’abord par la buse avant d’atteindre la sonde de température, si toutefois il arrive jusque là étant donné l’orientation différente.
Attention au serrage des buses !
L’impression du grand sapin montré plus haut s’est faite en deux tentatives. Lors du premier essai, une des buses est légèrement descendue dans son logement, ce qui a engendré un décalage en Z de cette tête et rendu impossible la cohésion de couche avec la couleur suivante. L’impression a été avortée.
Suite à cette déconvenue, j’ai remonté les buses en les serrant moins modérément dans l’espoir qu’elles ne glissent plus. Ce fut une erreur car les fragiles tubes des buses ont été écrasés, réduisant le diamètre interne et gênant/bloquant le passage des pointes de filament.
Les buses de Nextruder comportent deux petites gorges, dont une seule est utilisée sur la Prusa XL. Il faut pousser la buse en butée vers le haut, puis celle-ci est maintenue par une unique vis qu’il faut serrer très modérément à l’aide d’une clé. Il y a un tout petit jeu vertical de quelques dixièmes dans cette gorge, avant que la vis ne soit serrée.
Cette conception est très discutable car il y a deux forces opposées qui contraignent la buse :
- La force qui s’applique vers le haut lors du palpage, quand la buse touche le plateau. Cette force est contrée par la mise en butée lors du montage.
- La force qui s’applique vers le bas durant l’impression lorsque le moteur épaulé de sa démultiplication de 1:10 pousse le filament. Cette dernière est contrée uniquement par le serrage de la vis.
Au fil du temps et à force de dilatations thermique, cette vis peut se desserrer et la buse descendre de quelques dixièmes jusqu’à la butée opposée de la gorge. A noter que sur l’Original Prusa MK4S, les deux gorges sont utilisées avec deux vis moletées que l’on ne peut serrer que du bout des doigts. Ce système semble plus fiable.
Plateau chauffant
Le plateau chauffant est innovant. Il n’est pas constitué d’un seul plateau monolithique mais d’une matrice de 4×4, soit 16 tuiles indépendantes. Ce sont les mêmes tuiles qui sont utilisées sur les moins connues Prusa Pro AFS.
Comme pour le Nextruder, le plateau possède sa propre électronique de gestion et chaque tuile est contrôlée individuellement, ce qui permet de ne chauffer que la zone nécessaire à l’impression. C’est une idée astucieuse qui permet de faire des économies d’énergie. Le dessous du plateau est également isolé par une mousse afin de gagner encore un peu en rendement.
Ces tuiles sont montées sur des joints de dilatation afin de prévenir toute déformation de la zone d’impression, garantissant ainsi une planéité presque parfaite du plateau, quelle que soit la température. Les relevés thermiques montrent une très bonne homogénéité de la température sur toute la surface, environ +/-2°C d’écart entre les points chaud et froid.
De plus, lorsqu’une impression démarre, il y a une étape plus ou moins longue d’absorption de chaleur, environ 2 minutes pour le PLA, 7-8 minutes pour le PETG et même 11 minutes pour l’ASA. Cela permet aux 16 plateaux et à la steel sheet de se stabiliser, notamment en dilatation le temps de transférer la chaleur dans toute la masse. La mesure du maillage est effectuée seulement ensuite. Cette étape de stabilisation peut être passée pour gagner du temps, au détriment de la qualité de la première couche pour de grandes surfaces.
Phase Stepping / Bruit
L’Original Prusa XL bénéficie d’une technologie appelée Phase Stepping qui permet de réduire énormément les vibrations des moteurs et donc de considérablement réduire leur bruit. Malgré l’amélioration que cette technologie apporte, c’est une machine bruyante comparativement à une MK4S. Il y a deux types de bruits gênants : les déplacements rapides à vide et les changements d’outils.
Lors des déplacements rapides à vide la machine émet un sifflement assez strident que l’on entend aisément dans la pièce à côté malgré la porte fermée. Ce bruit disparait si l’on active le mode furtif, qui limite la vitesse et l’accélération.
Lors des changements d’outils, le mécanisme de préhension précédemment étudié produit des claquements secs et ceux-ci ne peuvent pas être atténués. Ils sont cependant moins gênants la nuit, porte close.
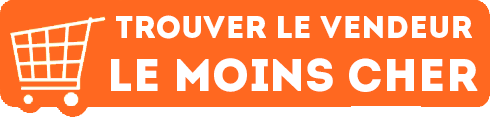
Améliorations et accessoires
Clé USB
La clé USB d’origine fonctionne très bien mais elle est de taille “normale”, ce qui est plutôt long en fait. Si vous utilisez la Prusa XL principalement en WiFi / Ethernet, je recommande l’usage d’une clé USB miniature qui restera à demeure et dépassera peu de l’écran. Non pas que ce soit problématique d’avoir une clé qui dépasse mais c’est moins esthétique et présente un risque d’accrochage, avec une manche par exemple.
Plateaux flexibles
De série, la Prusa XL est livrée avec une tôle flexible de finition “satinée” mais il est possible d’utiliser des tôles flexibles en finition “lisse” ou “texturée”. Il existe même une tôle spécifique pour l’impression de PA. Choisissez votre plaque en fonction de l’état de surface souhaité ou du type de filament que vous utilisez.
Buses
Parmi les “améliorations” possibles, on peut passer sur des buses “High Flow” afin d’augmenter le débit maximum et donc réduire les temps d’impression, ce qui est intéressant étant donné le volume maximal imprimable sur cette Original Prusa XL. On peut également passer sur des buses renforcées pour pouvoir utiliser des filaments abrasifs. Et, enfin, il existe un adaptateur Nextruder pour buses V6 qui ouvre tout le catalogue existant de buses V6 du marché.
Upgrades
Original Prusa XL Enclosure
Pour l’impression de filaments techniques, il sera indispensable d’opter pour une enceinte close. Prusa Research propose une upgrade : “Original Prusa XL Enclosure” disponible séparément ou en bundle avec l’imprimante. Nous ne connaissons pas son efficacité réelle mais comme nous l’avons vu lors des tests, l’impression de grandes pièces ne serait-ce qu’en ASA, n’est pas envisageable sans caisson.
L’Original Prusa XL Enclosure est directement intégrée sur la machine et permet d’avoir un environnement d’impression stable (chauffage passif) afin de pouvoir imprimer plus facilement des filaments sensibles tels que le l’ASA, le PC, le PA ou le PP. Cette enceinte filtre activement les particules ultra fines et est connectée à l’imprimante permettant l’accès aux paramètres de filtration directement depuis l’écran de la machine.
Voir les caisson Original Prusa Enclosure sur le comparateurRéflexions et conclusion
Si j’avais énormément d’attentes concernant cette Prusa XL que je suivais depuis son annonce, et même avant depuis les prémices du Toolchanger de E3D, je dois dire que je ne m’attendais pas à ça.
La technologie des Toolchanger est relativement récente et peu répandue dans le monde des imprimantes 3D. Cette Original Prusa XL en version cinq têtes est le résultat d’un long travail visant à rendre cette technologie suffisamment précise, fiable tout en étant techniquement abordable. A la publication de ce test, notre exemplaire cumule près de 300 heures d’impression, 15 000 changements d’outils et 1,6 km de filament (environ 5 kg) sans le moindre accroc de ce point de vue.
Pour avoir eu une IDEX, je sais combien le multi-têtes est complexe à mettre au point. Je sais que cette technologie de Toolchanger l’est encore plus à tous les niveaux (mécanique, firmware, slicer) et je dois dire que Prusa Research a effectué ici un travail de maître. La mise au point est très bonne dans le sens où l’on ne soucie pas de savoir si la machine est bien réglée : elle l’est.
Il y a cependant un niveau supplémentaire à mettre au point : l’utilisateur. En effet, cette technologie ouvre des possibilités excitantes mais amène aussi son lot de contraintes. Je pense par exemple au séchage des filaments qui est primordial, même pour un basique PLA, alors qu’on s’en soucie peu sur une imprimante 3D mono-tête. Mais il y a aussi la gestion des matières différentes au sein d’une même impression qui demande d’acquérir une certaine expérience.
D’une manière plus générale, cette Original Prusa XL en version multi-têtes (2T ou 5T), bien que ce soit une Prusa, nécessite une phase d’apprentissage. Il y a donc un contraste entre l’excitation d’avoir une machine innovante dont on sait qu’elle provient d’un fabricant réputé, et le temps nécessaire avant de bien intégrer toutes les subtilités pour en obtenir pleine satisfaction.
Vous l’aurez compris, cette Prusa XL s’adresse à un public plutôt très averti et n’est pas destinée à l’utilisateur lambda qui souhaite seulement imprimer une collection de figurines. Pour ça, il vaut mieux se tourner vers la MK4S et son MMU3 qui seront beaucoup plus abordables, techniquement et financièrement.
Public averti oui, mais professionnel ? Ca dépendra fortement du besoin. S’il s’agit de produire des pièces avec des filaments techniques, alors clairement la réponse est non. Du moins pas sans l’option caisson et là encore, sa température est limité (pas de chauffage actif). Hormis la Prusa Pro HT90 qui ne s’adresse pas aux particuliers et qui est clairement hors jeu niveau tarifaire, c’est là que Prusa prend du retard face à la concurrence. Les machines grand public actuelles possèdent des enceintes chauffées activement et peuvent même sécher les filaments tout en étant abordables financièrement (Qidi Plus4, Bambu Lab X1E + AMS…).
Le point fort de l’Original Prusa XL multi-têtes reste donc sa technologie de Toolchanger qui permet facilement d’utiliser des matières différentes, sans contamination croisée, avec une tour de déchet minime et un temps d’impression réduit. Sur ce segment précis, elle n’a pas de concurrence à ce jour.
Maintenant, j’ai un problème avec cette machine : je n’arrive pas à la positionner correctement entre sa classe technologique, ses performances et son tarif. A quel marché s’adresse-t-elle ? Le passionné qui veut un grand volume et peut se permettre d’acheter une machine premium ? Le petit professionnel qui n’a pas de besoin en matière technique ? Difficile à dire, d’autant plus que toute cette conclusion serait probablement très différente pour la Prusa XL mono-tête.
D’un point de vue personnel, je pense qu’opter pour l’Original Prusa XL en version deux têtes serait un bon compromis. Cela la ramène à un budget certes encore élevé (2599 €, 1100 € de moins que la version 5 têtes), mais déjà plus abordable pour la classer du côté amateurs et surtout pour profiter des avantages de cette technologie unique qu’est le Toolchanger.
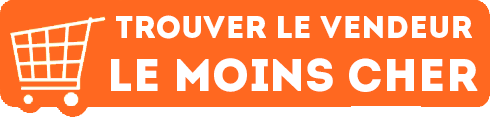
Notes et conclusion
Qualité d'impression - 9.4
Fiabilité - 9
Logiciel - 9.6
Utilisation - 9
Rapport qualité / prix - 8
9
/10
- Première couche parfaite sur toute la surface
- Technologie Toolchanger
- Plateau innovant
- Grand volume d'impression
- Matériel de qualité
- Châssis très rigide
- Réglages au point
- Click-to-Print USB/LAN
- Prix élevé
- Semi-assemblé = kit
- Montage des docks à revoir
- Faiblesse de design sur les buses
- Assez bruyante
- Pas de caisson d'origine
- Nécessite une prise en main